Position Summary:
This role is for a highly skilled and detail-oriented Facilities Supervisor responsible for overseeing maintenance operations in a regulated Good Manufacturing Practice (GMP) environment. The position ensures that all equipment, utilities, and facilities are maintained in a compliant, safe, and efficient manner to support manufacturing and laboratory operations.
ultrainnovative – Tackle rare and dynamic challenges
Work Model:
Core Lab & Ops: This role typically requires that the majority of the work be conducted on-site
Responsibilities:
- Supervise and coordinate daily activities of maintenance technicians and contractors, ensuring efficient task delegation and execution
- Ensure all maintenance work complies with GMP, safety, and environmental regulations
- Plan, schedule, and manage preventive and corrective maintenance schedules for GMP-critical equipment and systems to minimize downtime and ensure operational continuity
- Maintain accurate and timely documentation of maintenance activities in the Computerized Maintenance Management System (CMMS)
- Lead troubleshooting efforts and conduct root cause analysis for equipment failures, implementing corrective actions
- Collaborate with Quality Assurance, Manufacturing, and Engineering teams to ensure equipment and facility readiness for production and audits
- Participate in audits and inspections conducted by internal teams and regulatory agencies, providing necessary documentation and support
- Train and mentor maintenance staff on GMP procedures, technical skills, and best practices in maintenance planning and execution
- Support deviation investigations and CAPA management by providing technical input, maintenance history, and contributing to timely resolution and documentation
Requirements:
- Associate or bachelor’s degree in Engineering, Facilities Management, or a related field (or equivalent combination of education and experience)
- 6+ years of maintenance experience in a GMP-regulated pharmaceutical, biotechnology, or medical device environment
- 2+ years of supervisory or team lead experience in a maintenance or facilities role
- Strong knowledge of GMP, FDA, EMA, and other applicable regulatory requirements and industry standards
- Proficiency with CMMS (e.g. Blue Mountain, Infor EAM, Maximo) and Microsoft Office applications (Excel, Word, Outlook, PowerPoint)
- Excellent communication, leadership, and problem-solving skills with the ability to manage cross-functional collaboration
- Demonstrated experience in planning, scheduling, and executing preventive and corrective maintenance programs
- Familiarity with HVAC, clean utilities (e.g., WFI, clean steam, compressed air), and critical manufacturing equipment
- Experience supporting deviation investigations, root cause analysis, and CAPA implementation
- Ability to read and interpret technical drawings, equipment manuals, and engineering specifications
- Strong organizational skills and attention to detail in a fast-paced, compliance-driven environment
Physical Demands/Work Environment/Safety Considerations:
- Stand for extended periods of time with periodic stooping / bending / kneeling
- Ability to climb ladders and stairs of various heights
- Able to lift, push, pull up to 50lbs
- Work in a controlled environment requiring GxP gowning and wear protective clothing over the head, face, hands, feet, and body. This requires the ability to change clothes into appropriate gowning and personal protective equipment
- Certain tasks may require use of a respirator; medical clearance will be required in advance
- Must remove all make-up, jewelry, and contract lenses while in the manufacturing environment
- Working in temperature controlled environments (cold rooms)
#LI-CK1 #LI-Hybrid
The typical annual salary range for this full-time position is listed below. This range reflects the characteristics of the job, such as required skills and qualifications and is based on the office location noted in this job posting. The range may also be adjusted based on applicant's geographic location.
This position is eligible for annual bonus and equity incentives. Actual individual pay is determined by demonstrated experience and internal equity alignment.
Ultragenyx Pharmaceutical is an equal opportunity employer and prohibits unlawful discrimination based on race, color, religion, gender, sexual orientation, gender identity/expression, national origin/ancestry, age, disability, marital and veteran status, and any other status or classification protected by applicable federal, state, and/or local laws. Reasonable accommodation will be provided for all protected statuses or classifications protected by applicable law, including individuals with disabilities, disabled veterans, for pregnancy, childbirth, and related medical conditions, and based on sincerely held religious beliefs. Applicants can request an accommodation prior to accepting a job offer. If you require reasonable accommodation in completing this application, or in any part of the recruitment process, you may contact Talent Acquisition by emailing us at talentacquisition@ultragenyx.com.
See our CCPA Employee and Applicant Privacy Notice. See our Privacy Policy.It is unlawful in Massachusetts to require or administer a lie detector test as a condition of employment or continued employment. An employer who violates this law shall be subject to criminal penalties and civil liability.
Note to External Recruiters: All candidate activity and open positions are managed strictly through our Human Resources Department. Our Human Resources Department kindly requests that recruiters not contact employees/hiring managers directly in an attempt to solicit business and present candidates. Please note that failure to comply with this request will be a factor in determining a professional relationship with our organization. Submission of unsolicited resumes prior to an agreement set in place between the Human Resources Department and the recruiting agency will not create any implied obligation. Inquiries on developing a recruiting relationship with us, may be directed to: talentacquisition@ultragenyx.com.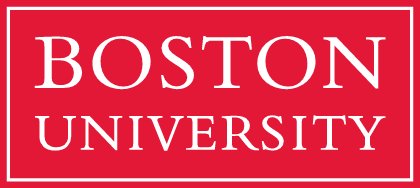
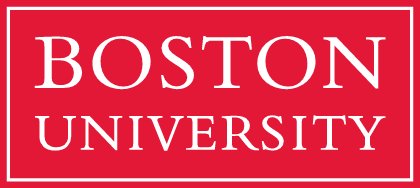
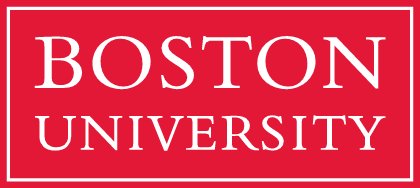